In a three-month period this year, Fayetteville-based rugged system solutions company Ozark Integrated Circuits (Ozark IC) officially received five Small Business Innovation Research awards to perform research projects with high commercial potential.
These awards include three Phase II contracts from the Department of Defense Air Force, NASA, and the Department of Energy and two Phase I contracts from the DOE and NASA.
The Arkansas Small Business and Technology Development Center provided important market research and assistance that Ozark IC used to help obtain these funded SBIR projects.
Several of the new awards are based on Ozark IC’s XNodesTM, or “Extreme Nodes.”
XNodes are single-board computers built on an advanced ceramic platform that are designed to operate in any condition. Each node is part of a family of devices that can be quickly combined and customized to address the needs of many markets and applications, from acquisition to actuation and closed-loop control, all with robust communication.
XNodes are based around different temperature ranges. For example, the 250 series of XNodes are designed to meet temperature ranges up to 250⁰C.
“The receipt of these five SBIR awards is obviously very welcome in these difficult times; they signify to us that the agencies regard our work as significant and needed,” said Matt Francis, Ozark IC’s founder and CEO. “This is an enormous encouragement to us and will help bring our products to market. We are very grateful.”
Objectives for the projects range from developing enhanced geothermal systems for deep directional drilling to creating a prototype multi-chip package for high-temperature, high-density electronic systems. To date, Ozark IC has received 22 SBIR/STTR awards totaling $9 million.
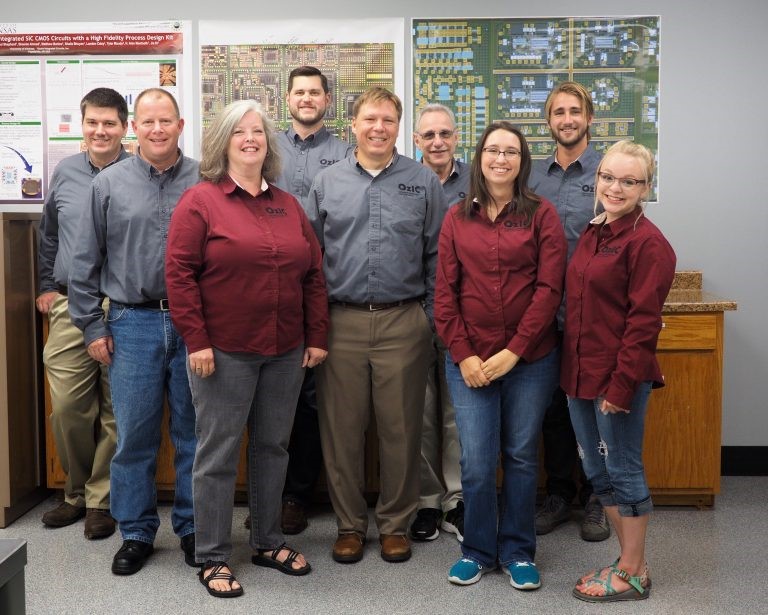
Air Force SBIR Phase II
The Air Force anticipates a growing use of electronic aircraft that will require effective operation at temperatures above the standard range of -55 to +125 degrees Celsius. There are currently no high-temperature and cost-effective extreme environment microcontrollers available for aerospace applications with operational lifetime exceeding 10,000 hours at high temperatures.
During its Phase II project, Ozark IC will design a test chip that allows characterization of the integrated circuit (IC) process to validate the lifetime and performance models projected during Phase I.
This project will culminate with the development and validation of a nominal 200⁰C, 250⁰C peak RISC-V based microcontroller as part of the 200 series of XNodes.
NASA SBIR Phase II
Complex electronic systems that can operate at high temperatures are necessary for space exploration, especially on the Venus surface (~470⁰C). A 500⁰C RISC-V microprocessor (used in the 500 series of XNodes) would be a fundamental computing building block for almost all space exploration functions (such as actuation, environment sensing, robotic motion etc.) on the Venus surface. High temperature environments that can use this computing building block are also found in rockets.
A high temperature computing building block that is central for environmental sensing and actuation is an essential component of many non-NASA applications such as jet engine control systems, hypersonic engines for flight and weapons, geothermal exploration, scientific experiments and production furnaces.
In this project, Ozark IC will create a 500⁰C RISC-V multi-chip system in package as a vehicle to illustrate the design procedures, the multi-chip package and the high-temperature components that go into creating a high-temperature electronic system.
DOE SBIR Ph II
Access to the earth’s subsurface requires technologies that can operate at extremely high temperatures and pressures. Enhanced geothermal systems require directional drilling deep into hot wells, with temperature profiles exceeding 325°C; while making better use of each well through techniques such as fracking and zonal isolation.
Establishing a well requires electronics that can withstand temperature/depth profiles and will be able to transmit critical telemetry to inform directional drilling.
During Phase I, Ozark IC successfully transitioned its data acquisition (AQ) XNode, AQ-100, to its high-temperature, high-density variant, the AQ-200, yielding a technology leap of 100ºC and an 87% reduction in size, both of which are critical enablers for downhole computing. Also during Phase I, Ozark IC identified a power/data transmission scheme for the down-hole electronics.
In Phase II, Ozark IC will produce prototypes of the AQ-200 and its wireline power/data plugin module, (AQ-200-WL) and assemble a 3-segment drillpipe mock-up to validate the connectors, cables, and electronics packaging schemes designed and prototyped during Phase I. This validation is the critical first step before manufacturing a volume of units that can support testing in geothermal, oil and gas fields.
In addition to its application in enhanced geothermal wells, results of this Phase II project will enable next generation oil and gas exploration and well monitoring. This technology has aerospace and automotive applications for improving engine performance and efficiency.
DOE SBIR Phase I
Both the Department of Energy and the private sector are interested in the prospect of nuclear power produced with advanced molten salt-cooled reactor, or MSR, designs. These salts are used to transfer heat from the reacting fuel or to have nuclear fuel dissolved within the salty fluid itself.
Continuous operation of MSR heat-exchange loops requires monitoring of the molten salt as it ages. Observations of the long-term operation of conventional salt heat-exchange loops show that loop components such as stainless steel pipes, flanges, pumps, and reservoirs introduce impurities as they corrode and produce fluorides. The electrical resistivity of these salts in their purest molten states is currently unknown.
Ozark IC will be designing and prototyping a molten-salt conductance sensor with enough precision to differentiate a pure sample of a molten salt (FLiBe) from a sample containing various concentrations of impurities. Ozark IC’s partner at the University of Wisconsin-Madison Thermal Hydraulics Laboratory will measure the electrical conductivity profile of FLiBe from 800°C down to its freezing point near 458°C. This measurement will provide the key requirement of a high-temperature module to make the same measurement remotely in a molten salt reactor.
In addition to molten salt heat exchange loops, commercial applications for this sensor include high-temperature chemical analysis and geothermal well logging.
NASA SBIR Phase I
NASA seeks to land instruments on the corrosive, high-pressure, high-temperature surface of Venus. NASA Glenn Research Center’s silicon carbide (SiC) JFET-R technology is the only one that has shown 1000’s of hours operation under Venus surface conditions. Due to the extreme environment found on the surface of Venus, access to reliable passive components such as resistors and capacitors to accompany JFET-R chipsets are minimal to not available.
There have been limited design options for mixed signal application specific integrated circuits due to their dependency on off-chip passive components.
In this project, Ozark IC will develop an all JFET-R based analog to digital converter with supporting passive components in a single integrated package. Once resistor materials have been selected, resistor test structures will be printed. These designs will be evaluated at probe to 400˚C as well as long term reliability testing at 500˚C. These components will be used with the 500 series of XNodes.